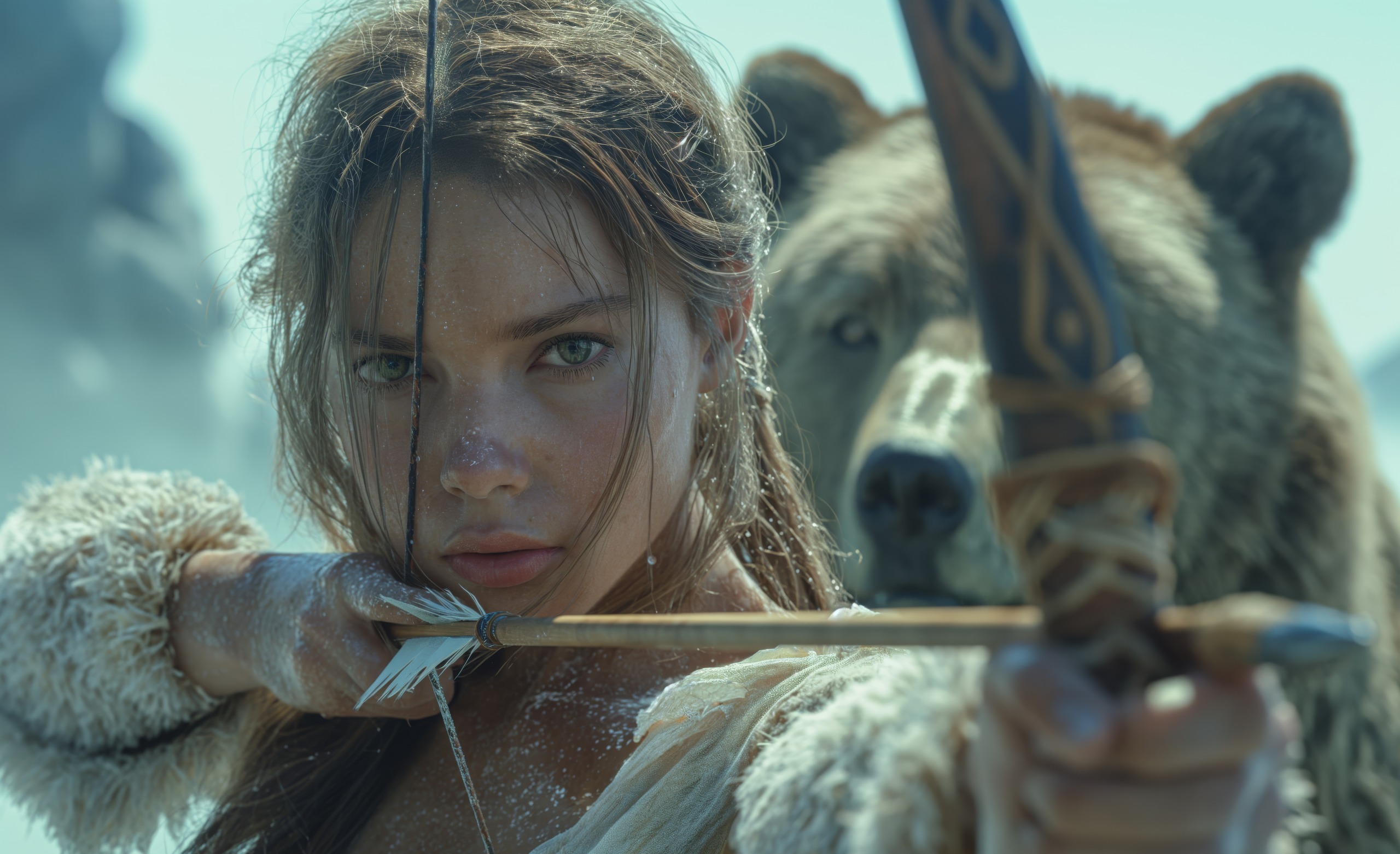
How To Make A Bow And Arrow
Whether you’re looking for a new hobby or want to embrace traditional craftsmanship, learning how to make a bow and arrow can be both fulfilling and exciting. The ancient art of bow and arrow making is not just a skill; it’s a journey back in time.
Imagine crafting your very own weapon that has stood the test of millennia, connecting you to hunters, warriors, and archers throughout history. This age-old practice allows you to tap into creativity while honing practical skills.
Picture yourself selecting the perfect wood, shaping it with your hands, and ultimately shooting an arrow you’ve crafted yourself. The feeling of accomplishment is unmatched! If you’re ready to dive into this captivating craft, keep reading as we guide you through every step of creating your own bow and arrows from scratch.
Materials Needed for Making a Bow:
When it comes to making a bow, choosing the right materials is crucial. Start with wood selection. Traditional options include yew, hickory, and oak. Each type has unique properties that affect flexibility and strength.
Next, gather your tools. A saw will help you cut the wood to size, while a draw knife or rasp can refine its shape. You’ll also need a string-making tool to create an effective bowstring.
Don’t forget about adhesives if you’re planning on adding any additional components or reinforcing sections of your bow. Some makers prefer natural glues for authenticity.
Consider protective gear like gloves and goggles when using sharp tools and handling heavy pieces of wood. This ensures both safety and comfort throughout your project as you embark on this creative journey.
– Wood selection
Selecting the right wood is crucial for making a bow. Different types of wood offer varying levels of flexibility and strength, which directly impact performance.
Look for woods like yew, hickory, or elm. Yew has been used for centuries due to its excellent tensile strength and elasticity. Hickory is another popular choice known for its durability and resilience.
Consider the grain of the wood as well. Straight grains provide better stability while knots can weaken your bow’s structure. Inspect each piece carefully before committing to it.
It’s also wise to think about local availability. Sometimes using native woods not only supports sustainable practices but also helps you connect with your environment in a unique way.
Each type brings distinct characteristics that influence how your finished product will feel when drawn back and released. Choose wisely; this step sets the foundation for all future crafting efforts.
– Tools required
When it comes to crafting your own bow, having the right tools is essential. A few basic items will set you on the path to success.
First, a sturdy saw is crucial for cutting down your chosen wood. A hand saw or band saw can work wonders here.
Next, a draw knife will help shape and taper your bow limbs with precision. This tool allows for clean cuts and smooth finishes.
Don’t forget about sandpaper or a rasp; these are key for refining the surface of your bow until it’s just right.
A tillering stick is also helpful to measure and adjust the bend of your bow as you craft it, ensuring optimal performance when shooting.
Clamps or vices will hold everything securely in place while you work on fine-tuning each element of your creation.
Step-by-Step Guide on Making a Traditional Bow
Step 1: Choosing the Right Wood
Choosing the right wood is crucial for creating a traditional bow. The type of wood you select will directly affect the bow’s strength, flexibility, and overall performance.
Look for woods known for their elasticity and durability. Popular choices include yew, osage orange, hickory, and bamboo. Each has unique characteristics that can enhance your project.
Consider the grain pattern as well. A straight grain provides consistent bending properties while avoiding weak points in the material. Inspecting each piece closely ensures you pick one with minimal knots or imperfections.
Climate plays a role too; certain woods may perform better depending on humidity levels where you’ll be using your bow. Research local availability to make an informed choice that suits both your crafting needs and shooting conditions.
Gather samples if possible before making a final decision—feeling the weight and texture helps visualize how it might shape up into a beautiful weapon of skill.
Step 2: Measuring and Cutting the Bow Stave
Measuring and cutting the bow stave is a critical part of traditional bow making. Precision at this stage sets the foundation for your entire project. Start with selecting a straight piece of wood, ideally between six to eight feet long.
Using a measuring tape, mark out your desired length on the stave. For most bows, aim for about 68 inches from tip to tip.
Once marked, grab your saw. A fine-tooth hand saw works well here; it allows for more control than power tools. Cut along the line you made earlier, ensuring that you maintain a steady hand.
After cutting, check both ends of the stave for any rough spots or splinters—smooth them down with sandpaper as needed. This will help in shaping later on and ensures that you have an even base to work from throughout the process.
Step 3: Shaping the Bow Stave
Shaping the bow stave is where creativity and craftsmanship come together. You start with an unrefined piece of wood, full of potential. Your goal is to transform it into a functional work of art.
Begin by carefully removing excess material from both sides using a drawknife or rasp. Pay attention to the grain; this will influence how your bow performs later on. Shape it gradually, following its natural contours for balance and strength.
Focus on achieving an even profile from tip to tip. The belly (the side that faces you when drawn) should be slightly rounded, while the back needs to remain flat or have minimal contouring.
Remember to take breaks often. Step back and assess your progress frequently—this ensures you’re aligned with your vision for the final product. It’s all about patience and precision as you mold that piece of wood into something extraordinary.
Step 4: Tillering the Bow
Tillering is a crucial step in the bow-making process that ensures your bow will perform optimally. At this stage, you’ll focus on achieving a balanced bend across the entire stave.
Begin by using a tillering stick. This tool helps visualize how the bow flexes as you draw it back. Attach one end of your string to the tip of the stave and pull gently to see how each limb bends.
Take note of any irregularities in shape or depth. If one side bends more than the other, carefully remove wood from the stiff areas with a rasp or knife.
Continue checking and adjusting until both limbs curve evenly when drawn. Patience is key here; rushing can lead to an unbalanced bow that won’t shoot straight.
Remember, proper tillering not only enhances performance but also contributes to safety during use. Enjoy this delicate dance between art and science!
Step 5: Stringing and Finishing the Bow
Now it’s time to bring your traditional bow to life by stringing it. Start by choosing the right type of bowstring. Material options often include Dacron or fast flight, depending on your preference and bow weight.
Carefully measure out the length needed for your string, taking into account the bow’s unstrung length plus a little extra for tying off knots. Use a reliable serving tool if you want added durability at the nocking points.
Once your string is prepared, attach one end securely to one limb of the bow. Then slowly bend the other limb back while attaching that side of the string as well. This process requires patience; go slow to avoid twisting or damaging any part of your creation.
After you’ve strung it up, inspect everything closely. Look for uniform tension across both limbs and make necessary adjustments before testing its draw weight. Your hard work is about to pay off!
Tips for Choosing the Right Arrows
Choosing the right arrows is crucial for effective archery. Start by considering your draw weight; heavier bows require stiffer shafts to maintain accuracy and prevent damage.
Next, think about the length of your arrows. Measure from the nock point to a spot just past your longest finger when at full draw. This ensures that they are not too long or short for optimal performance.
Pay attention to arrow material as well. Aluminum offers durability while carbon provides lightweight flexibility. Each has its own benefits depending on how you plan to use them.
Don’t overlook fletching style either. The type and number of vanes can affect stability in flight, with three fletches being most common for balance and control.
Consider where you’ll be shooting—target competitions may have different requirements compared to hunting scenarios. Choose wisely based on your needs!
Materials Needed for Making Arrows:
When crafting arrows, the right materials make all the difference. Start with selecting your shaft. Traditionally, wood is favored for its natural flexibility and sturdiness. Popular choices include cedar or pine due to their lightweight characteristics.
Next, consider using carbon fiber shafts if you seek performance and durability. They resist bending and ensure consistency in flight.
Arrowheads are crucial as well. Steel tips offer excellent penetration for hunting purposes, while broader heads are ideal for target shooting. You may also explore fletching options like feathers or plastic vanes that stabilize your arrow’s flight.
Don’t overlook nocks too—these small notches at the end of each shaft fit securely onto your bowstring, ensuring a proper release every time you shoot. With these components chosen wisely, you’ll be ready to craft arrows that fly true and hit their mark effectively.
– Shaft selection
When selecting a shaft for your arrows, consider the material first. Options typically include wood, aluminum, and carbon fiber. Each has its own characteristics that affect performance.
Wood shafts offer a traditional feel and can be handcrafted to suit personal preferences. They tend to be heavier but provide great stability in flight.
Aluminum shafts are lightweight and very durable. They resist bending or breaking under pressure but may lack some of the natural aesthetics found in wooden arrows.
Carbon fiber is an excellent choice for those seeking high performance. It’s incredibly strong yet light, making it ideal for serious archers aiming for precision.
Next, focus on spine stiffness. The right spine ensures your arrow flexes properly when shot, impacting accuracy significantly. A stiffer shaft works well with powerful bows while more flexible options benefit lighter setups.
Take time to test different materials and spines to find what complements your shooting style best.
– Arrowhead selection
Choosing the right arrowhead is crucial for both performance and safety. The type of arrowhead you select depends on your intended use, whether for target practice or hunting.
Broadheads are popular among hunters. They have sharp blades that create a larger wound channel, increasing their effectiveness in the field. For target shooting, field points work well as they offer better aerodynamics and can be reused without dulling.
Consider material too. Steel heads are durable but heavier, while aluminum options provide a lighter feel. Some archers prefer carbon-tipped heads for their balance between weight and strength.
Don’t forget to match the arrowhead size with your shaft diameter for optimal flight stability. Test different types to see which works best with your bow setup; each combination may yield varying results when it comes to accuracy and penetration power.
Step-by-Step Guide on Making Arrows
Step 1: Preparing the Shaft
Preparing the shaft is a crucial first step in crafting quality arrows. This component directly impacts your arrow’s flight and accuracy.
Start by selecting the right material. Common choices include wood, aluminum, or carbon fiber. Each has unique qualities that affect weight and performance.
Once you have your preferred material, cut it to the desired length. Standard arrows typically range between 28 to 32 inches, but personal preference plays a key role here.
Next, smooth out any rough edges using sandpaper or a file. A clean finish not only looks better but also helps with aerodynamics during flight.
Drilling an insert hole at one end for nocking is essential too. Make sure it’s precise; this ensures proper alignment when attaching the nock later on.
Your preparation sets the foundation for success in archery!
Step 2: Fletching or Adding Feathers to the Arrow
Fletching is a crucial step in the arrow-making process. It involves attaching feathers or vanes to stabilize the arrow’s flight. Proper fletching ensures accuracy and consistency, making it an essential skill for any archer.
When selecting feathers, you can opt for natural materials like turkey or goose feathers, or synthetic options that offer durability. Each type has its unique benefits. Natural feathers are lightweight and traditional but might require more care.
To attach the fletchings, use a quality adhesive designed for archery equipment. Ensure that each feather is aligned correctly; typically, they should be spaced evenly around the shaft. A common arrangement includes three fletches—two at 120 degrees apart and one positioned directly opposite.
Be mindful of your grip when applying pressure to secure them in place. Let them cure fully before moving on to nocking or adding tips; this will guarantee better performance during your shooting sessions.
Step 3: Nocking the Arrow
Nocking the arrow is a crucial step in ensuring your shot flies true. This part connects your shaft to the bowstring, so precision matters. Start by locating the nock, which is a small plastic or wood piece that fits onto the string. It usually has a groove on one side to keep it secure.
Position this groove away from the fletching; this helps maintain proper orientation during flight. Slide the nock onto your arrow’s end until you hear a satisfying click. This indicates it’s firmly attached and ready for action.
Checking alignment is key here too—make sure everything sits straight and snug against each other. A well-nocked arrow can greatly enhance accuracy, making every shot feel more effortless than before.
With this step complete, you’re closer to crafting arrows that will perform beautifully when you take aim at your target!
Step 4: Adding Tips or Points to the Arrow
Once your shaft is prepared and fletched, it’s time to add the tip or point. This step is crucial for determining how your arrow will perform in flight and impact.
Choose from various types of tips based on your intended use—target shooting, hunting, or recreational archery. Broadheads, field points, and blunt tips offer unique benefits tailored to different activities.
Before attaching a tip, ensure that the end of the shaft is clean and free from debris. Most tips come with a screw-in design that allows for easy attachment. If you’re using glue-on points, apply an even layer of adhesive before securely placing the tip onto the shaft.
Allow any adhesive to cure fully as per manufacturer instructions. Properly secured points enhance accuracy and control during release while ensuring durability through multiple shots against targets or game animals.
Customizing Your Arrows with Paint or Designs
Customizing your arrows can be as fun as shooting them. It’s a chance to express your personality and style. Start with quality paint designed for outdoor use. Acrylic or spray paints work well, but ensure they adhere to the arrow material. Choose colors that reflect your individuality or even match your bow.
Using stencils can add intricate designs or patterns. Floral motifs, geometric shapes, or tribal prints can make each arrow stand out in a unique way. Just remember to let the paint dry completely before handling them again. Adding personal touches like your name or initials can also enhance their appeal.
Stickers are another quick option; just make sure they’re durable enough for outdoor conditions. Don’t forget about safety! Make sure any added weight from decorations doesn’t affect flight performance adversely. Customization is all about making it yours while maintaining functionality on the range or field.
Safety Precautions When Handling Bows and Arrows
Safety is paramount when handling bows and arrows. Always treat your bow as if it’s loaded, even when you believe it’s not in use. Before shooting, ensure your surroundings are clear of people or obstacles. This helps prevent accidents that could lead to injury.
A designated target area is ideal for practice sessions. When drawing the bowstring, keep fingers away from the path of the string. An unexpected release can cause serious harm. Always wear appropriate protective gear, such as arm guards and finger tabs.
These items help shield against potential injuries while shooting or drawing. Check your equipment regularly for damage. A cracked bow or faulty arrow can turn a fun experience into a dangerous one quickly.
Educating yourself about proper techniques also contributes significantly to safety. Familiarizing yourself with best practices will enhance both your skills and security while enjoying this timeless sport.
Alternatives to Traditional Bow Making
If traditional bow making feels daunting, there are several modern alternatives to explore. One popular option is using composite materials. These can provide greater flexibility and durability without the extensive craftsmanship involved in wooden bows.
Another alternative is purchasing pre-made kits. Many companies offer comprehensive packages that include all necessary components. This approach allows beginners to focus on assembly rather than sourcing individual materials.
For those interested in a more high-tech route, consider 3D printing your bow. With access to a printer and digital designs, you can create customized equipment tailored to your preferences. Take advantage of online tutorials and workshops focused on modern archery equipment.
Engaging with experienced instructors or communities can enhance your skills while introducing innovative techniques for crafting bows and arrows.
Conclusion
Creating your own bow and arrow can be a rewarding experience. It not only connects you to ancient traditions but also allows for personalization in design and function. Whether you’re crafting a traditional bow or selecting the perfect materials for arrows, each step adds to the satisfaction of using something you’ve made yourself. Remember that safety is paramount; always handle your equipment with care.
As you explore this craft further, consider experimenting with various styles and techniques to enhance your skills. You may discover new preferences or even create unique designs that reflect your personality. Engaging in bow making can also spark an interest in archery as a hobby—providing both relaxation and challenge.
Dive into this creative venture, gather your materials, and let the process unfold. The journey of making bows and arrows is just as exciting as mastering their use!
Hi Jack, this guide breaks down each step, from shaping the bow to making arrows and adding fletching (feathers for stabilization), which helps someone like me visualize the process. However, I wonder if I’d have the patience and precision required, especially when it comes to carving the notches and ensuring everything is aligned correctly.
Hey Zain,
Thank you for stopping by and sharing your thoughts with us today. Making a bow and arrow is an art and not easy for a beginner. With that being said, I would only attempt a project like this if you are comfortable with woodworking. You don’t really need to have prior experience making a bow and arrow but it would definitely help. Please come back and share your experience making your own bow and arrow. Thanks again for stopping by. Best wishes and good luck should you attempt this project.