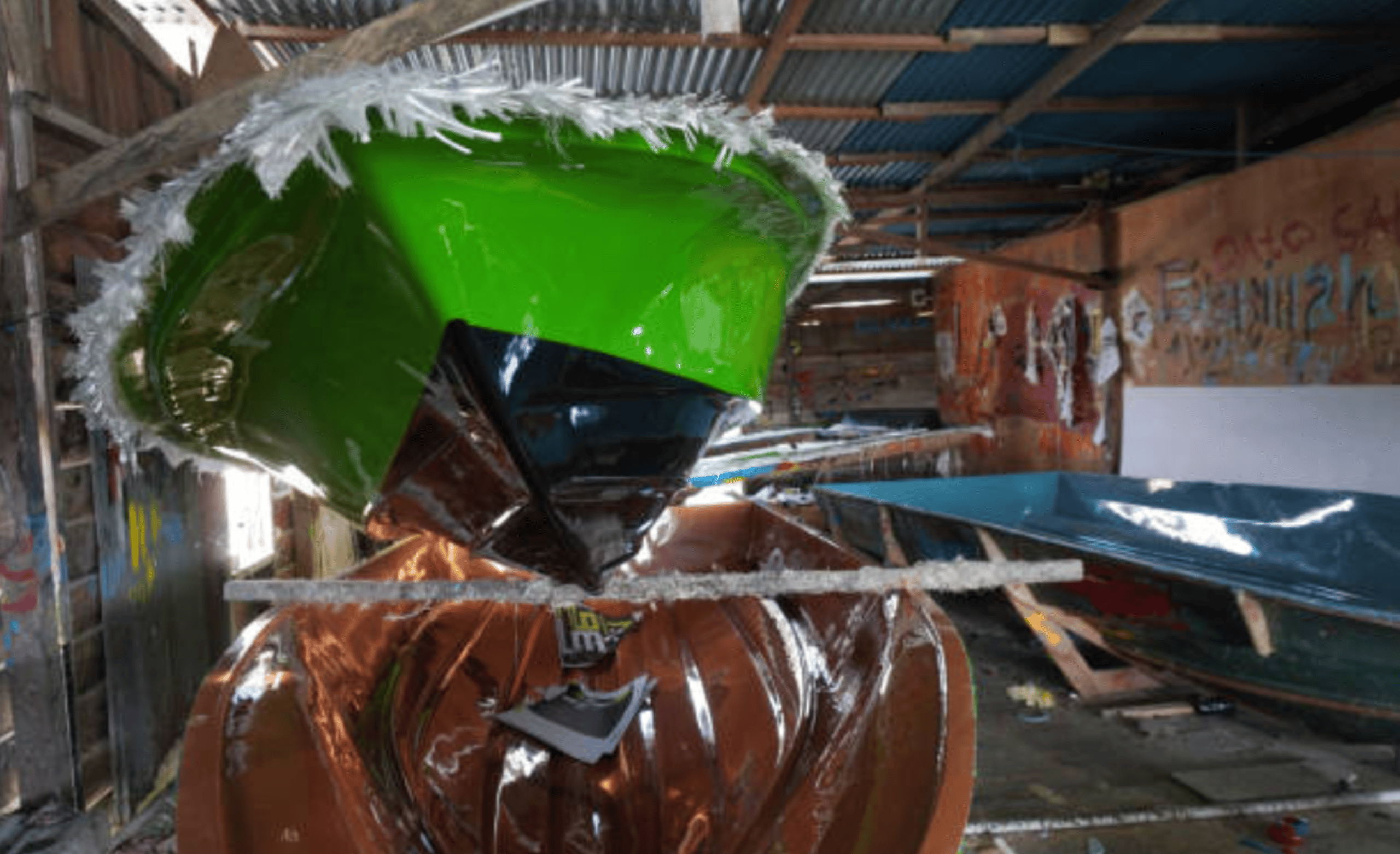
How To Build A Fiberglass Boat Mold
Understanding how to build a fiberglass boat mold opens up endless possibilities for creating custom designs tailored to your boating needs. Building a fiberglass boat mold is an exciting venture that combines craftsmanship with creativity.
Whether you’re a seasoned boat builder or just starting your journey in marine construction, mastering the art of mold creation can be immensely rewarding. Fiberglass is known for its durability and lightweight properties, making it the perfect material for crafting boats that glide smoothly across the water.
From sleek racing vessels to cozy fishing crafts, having your own mold allows you to bring your unique vision to life. With the right tools and techniques, anyone can embark on this journey and produce high-quality molds that stand the test of time.
Ready to dive into the world of fiberglass boat mold building? Let’s explore what it takes!
Materials Needed for Building a Mold
To build a fiberglass boat mold, you’ll need several key materials. Start with a quality plug material, which could be foam or wood. This forms the shape of your final boat. Next, gather your fiberglass cloth and resin. Epoxy or polyester resins are popular choices due to their strength and durability.
Don’t forget gelcoat for that smooth finish; it’s crucial for both aesthetics and function. Ensure you have plenty of release agent as well; this will help separate the mold from the plug without damage. You’ll also require tools like brushes, rollers, mixing containers, and safety gear such as gloves and masks.
Consider having sandpaper on hand for surface finishing touches before pouring in any layers. Each material plays its role in making sure your mold comes out just right.
Step-by-Step Guide on Building a Fiberglass Boat Mold:
#1. Preparing the Work Area
Before diving into the mold-building process, it’s crucial to set up your work area properly. A clean and organized space can make a significant difference in efficiency and quality.
Start by choosing a well-ventilated location. Fiberglass materials emit fumes that need to dissipate for safety. Ensure you have adequate lighting, so you don’t miss any details during construction.
Next, gather all necessary tools and materials nearby. This includes mixing containers, brushes, rollers, and safety gear like gloves and goggles. Having everything at hand minimizes interruptions while working on your project.
Clear away any debris or distractions from the workspace. A clutter-free environment helps maintain focus as you tackle each step of constructing the mold.
Consider laying down protective coverings on surfaces to prevent damage from spills or drips during the fiberglass application process. Setting up an efficient workspace sets a solid foundation for success ahead.
#2. Creating a Plug for the Mold
Creating a plug is one of the most critical steps in building a fiberglass boat mold. The plug serves as the original shape from which your mold will be formed, so accuracy is key.
Start by selecting materials that are easy to work with. Plywood or foam can serve as great bases. Shape it according to your desired boat design, ensuring all curves and dimensions reflect your vision.
Once you have the base ready, apply layers of filler and sand for smoothness. This step might take time but getting this right ensures an excellent finish on the final product.
After achieving a flawless surface, seal it properly to prevent any damage during molding. A well-prepared plug sets the foundation for a successful mold-building process and ultimately influences the quality of your finished fiberglass boat.
#3. Constructing the Mold Box
Constructing the mold box is a crucial step in building your fiberglass boat mold. This structure will hold everything together, ensuring precision and stability throughout the process.
Start by selecting materials such as plywood or MDF for durability. Cut the pieces to size based on your plug dimensions. Make sure to measure twice; accuracy is vital here.
Once cut, assemble the sides using screws or strong adhesive. Reinforce corners with brackets for added support, particularly if you’re working with larger molds. A sturdy base is essential to prevent warping during curing.
Leave some space around your plug within the box for resin flow and proper ventilation after applying gelcoat and fiberglass layers. Ensure all joints are sealed properly to avoid any leaks that could compromise your work later on.
After constructing the frame, check for levelness before moving on to applying gelcoat. Every detail counts at this stage!
#4. Applying Gelcoat and Fiberglass Layers
Applying gelcoat is a crucial step in creating your fiberglass boat mold. This layer serves as the surface finish, providing a smooth and durable finish for your mold. Start by mixing the gelcoat according to manufacturer instructions, ensuring it’s thoroughly blended.
Use a brush or roller to apply an even coat over the prepared plug. Ensure complete coverage, paying attention to corners and edges where bubbles might form. Allow this initial layer to cure until it’s tacky but not fully hardened.
Next comes the application of fiberglass layers. Cut fiberglass fabric into manageable pieces that will fit well onto your plug without excessive overlap. Mix resin with hardener and saturate each piece before carefully laying it down on top of the gelcoat.
Smooth out any air pockets or wrinkles using a squeegee or roller, working from the center outward for an even layup. Repeat this process, adding multiple layers for strength and durability as required.
#5. Finishing Touches and Curing Process
Once the fiberglass layers are in place, it’s time to focus on the finishing touches. Inspect your mold for any imperfections or rough spots that need attention. Sanding smooths out these areas, ensuring a clean surface for future boat builds.
Next, apply a layer of wax to enhance the release properties of your mold. This step is crucial; it prevents sticking and allows for easy demolding later on. Use quality release agents for optimal results.
Curing is essential at this stage. Allow your mold to cure according to the manufacturer’s guidelines—typically 24 hours or more depending on conditions like temperature and humidity.
Place it in an environment with stable temperatures during curing; drastic changes can affect its integrity. After curing, check again for any flaws before moving onto production-ready status.
#6. Releasing the Mold from the Plug
Once the mold has fully cured, it’s time to release it from the plug. This part requires patience and care.
Start by checking for any overhangs or areas where the mold might be sticking. A gentle tap can help loosen stubborn spots. Use a plastic scraper to carefully work around the edges of the mold. It’s crucial not to damage either surface during this process.
Applying a bit of lubricant can ease the separation. A thin layer of wax or even silicone spray may do wonders in ensuring a smooth release.
As you lift, remember that molds can be heavy and awkwardly shaped. Having an extra pair of hands nearby is beneficial here.
Take your time, as rushing could lead to cracks or tears in your new fiberglass mold. Once free, inspect both surfaces for any imperfections before moving on with production plans.
Tips and Tricks for a Successful Mold Building Process
When building a fiberglass boat mold, preparation is key. Start with a clean workspace to avoid contaminants in your mold. Use high-quality materials for the best results. This includes gelcoat and fiberglass cloth. Investing in good products pays off.
Don’t rush through the curing process. Allow sufficient time for each layer to set properly before moving on to the next step. Patience during this phase can prevent future issues. Consider using vacuum bagging techniques for an even finish.
This method helps eliminate air bubbles and ensures better adhesion between layers. Document each step of your process. Keeping a detailed record will help you troubleshoot any problems that arise and improve your technique over time.
Common Mistakes to Avoid
When building a fiberglass boat mold, several common mistakes can hinder your progress. One major error is skipping the preparation of the work area. A cluttered space leads to distractions and possible contamination. Another frequent pitfall is not creating an accurate plug for the mold.
Precision in this step ensures that your final product will meet design specifications. Failing to apply gelcoat evenly is another concern. Uneven layers can lead to weak points in the mold, compromising its integrity over time. Many also underestimate curing times, rushing through this critical phase while sacrificing quality.
Patience pays off here; allowing adequate curing results in stronger molds. Neglecting safety precautions can have serious consequences. Always wear protective gear and ensure proper ventilation during the process to avoid health risks associated with chemicals used in fiberglass production.
Using the Mold for Boat Production
Once your fiberglass boat mold is ready, it’s time to put it to work. This step is where creativity meets craftsmanship. Start by applying a release agent inside the mold. This ensures that your finished product comes out cleanly without any damage.
Next, lay down layers of fiberglass cloth along with resin for strength and durability. Pay attention to detail; this will impact the final quality of your boat. After curing, carefully remove the newly formed hull from the mold. Handle it gently; even minor bumps can cause imperfections.
Inspect for any flaws before proceeding with sanding and finishing touches. A smooth surface not only looks great but also enhances performance on water. With everything in place, you’re ready for assembly or additional fitting as desired. Each build brings new opportunities and challenges that expand your skills further into boat production.
Safety Precautions to Consider
When working with fiberglass, safety is paramount. Always wear a mask to protect against inhaling fumes and dust particles. Proper ventilation in your workspace can make a significant difference in air quality. Gloves are essential when handling resin and other chemicals.
Skin contact can lead to irritation or allergic reactions, so choose high-quality nitrile gloves for protection. Safety goggles should be part of your gear as well. They shield your eyes from splashes that could cause serious damage during the mold-making process.
Don’t forget about protective clothing. Wear long sleeves and pants made from durable fabrics to avoid skin exposure while mixing materials. Keep a first-aid kit handy. Accidents can happen even with precautions in place, so being prepared will help you handle any minor injuries quickly and effectively.
Conclusion: Building a Fiberglass Boat Mold
Building a fiberglass boat mold can be a rewarding project for anyone interested in boating and craftsmanship. With the right materials, preparation, and attention to detail, you can create a durable mold that will serve as the foundation for your fiberglass boats.
Each step—from preparing your work area to applying gelcoat—is critical for achieving high-quality results. If you follow this guide closely and incorporate the tips provided, you’ll minimize errors and enhance your chances of success. Remember that patience is key throughout this process.
The curing time may require some waiting, but it’s worth it when you see the final product take shape. As with any skilled endeavor, practice makes perfect. Don’t be discouraged by early mistakes; instead view them as learning experiences that contribute to your growth in boat building.
Now it’s time to get started on creating your own fiberglass boat mold! Your journey into quality craftsmanship awaits.